-
蒸馏 常减压蒸馏
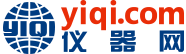
常压蒸馏和减压蒸馏习惯上合称常减压蒸馏,常减压蒸馏基本属物理过程。原料油在蒸馏塔里按蒸发能力分成沸点范围不同的油品(称为馏分),这些油有的经调合、加添加剂后以产品形式出厂,相当大的部分是后续加工装置的原料,因此,常减压蒸馏又被称为原油的一次加工。
常减压蒸馏装置中的每一个装置都是都是根据具体流程图和原理来设置的,不同的工艺流程图具有不同的使用用途。在制造使用过程中,人们的预期目的是提高蒸馏效果和提升炼油水平,并保证各项装置的性能,Z大化利用原油资源。
常减压蒸馏装置包括常压蒸馏装置和减压蒸馏装置,前者所利用的是热气化,来分馏冷凝原油,以获得用于社会生产和人们生活的汽油、采油以及煤油。后者在使用过程中会用到一定数量的加热原料,并要在真空的条件下分馏冷凝原油,然后再对其进行减压蒸馏,再加入其它的工序分裂原油性质,对其进行裂化处理来获得润滑油。
减压蒸馏装置能够有效提升炼油效果,减少操作成本。初馏塔和闪蒸塔都是我国原油蒸馏装置中的设备,其能够汽化和蒸出原油,达到减少热负荷的目的。
常减压蒸馏技术发展到现如今,虽然为我国的炼油事业做出了巨大贡献,但其在减压蒸馏技术方面还需要改善和更新。我国现阶段所拥有的此项技术还处于初级阶段,还没有掌握和运用其真正的技术,尤其是在沸点割切点的设置上与国际水平相比,还存在较大差距。并且,当前的蒸馏装置中的设备还处于老旧化状态,急需要对其进行深层次发展。
1、油气分压与温度
在减压蒸馏技术的使用过程中,其拔出率会受到油气气压和温度的影响,此处的油气气压与温度主要是指减压塔进料段处的。据相关实践表明,进料段的温度与拔出率呈正相关,烃分压与气化率呈负相关,减压炉出口温度与油品分解呈负相关。并且如果温度过高,会出现结焦问题。
2、雾沫夹带量
雾沫夹带量也主要存在于进料段,其对减压蒸馏技术的影响主要表现在减压塔蜡油的产品质量上。如果在闪蒸段上出现了夹带油滴,塔内件会出现严重的结焦问题。
3、工艺流程
常减压蒸馏装置的工艺流程也会对减压蒸馏技术产生一定影响。以530℃的拔出温度为例,如果在工艺流程方面没有考虑减压蒸馏技术的具体操作和减底急冷油流程,也没有对温度进行有效控制,那么当装置运行一段时间后便很容易出现结焦问题。工艺流程的完善程度直接决定蒸馏装置的运行周期,并会对塔顶真空度产生一定影响。
4、减压炉出口温度
在我国现有的减压炉出口温度的设置上,没有严格计算各类原油及其对应的加热炉结构,减压炉出口温度的设置大多是按经验进行的,这种设置方法存在炉管结焦隐患。
为了降低隐患风险,就需要将减压炉的分支温度和减压塔的汽化段温度分别设置在400℃和385℃以下,并减少渣油的热裂化反应。要想保护炉管,减轻炉压负荷,增加拔出率,就必须提高减压炉出口温度。
5、汽化段真空度
汽化段的真空度会受到塔顶真空度和塔内件压降的限制。塔顶真空度与汽化段真空度呈正比,塔内件压降与企划段真空度呈负相关。
1、常压蒸馏设备
常压下的原油蒸馏,所用的蒸馏设备为原油常压精馏塔。为了使石油中的重油在低温下沸腾、蒸发,所以在蒸馏的过程中,保持向蒸馏原油中通入高温水蒸汽,以降低石油气体的分压。但是要消耗很多蒸汽和增加冷却水的量,因此与减压配合更好。
石油蒸馏,通常塔底部的提馏段温度在350℃左右,不设置重沸器。通常向底部吹入少量的400~450℃,大约3MPa的过热水蒸汽,为了降低塔内的石油气分压,使混入重油中的轻组分蒸发。
在常压塔的旁边设置几个侧汽提塔,汽提塔重叠,但彼此分开,侧线的产品从常压塔中部抽出,送入上部的汽提塔,从该塔下部注入水蒸气,汽提出的低沸点成分与水蒸气从汽提塔顶部回主塔,侧线产品则送出装置。
从精馏塔上部引出部分液体热油,和其他冷流换热或冷却后返回塔,返回口高于抽出口2~3层板。在相同处理量下塔直径缩小,或在相同塔直径下可以提高塔的处理能力,可回收高温热源的这一部分。
2、减压蒸馏设备
为了提取更多的轻质组分,在压力不到100kPa的负压条件下,减少了被蒸馏的原料油沸点范围。低于大气压的压力下加热重油,高沸点馏分在低温蒸发,以避免高沸点馏分的裂解。塔底部是沸点为500℃以上的减压渣油。
减压蒸馏的核心设备是减压蒸馏塔和蒸汽喷射器。将塔内不凝气体和吹入的水蒸气不断地抽走以确保减压塔的压力降至几千帕,从而提高蒸发部分的真空度。
塔内压力较低,一方面使气体体积增大,塔直径大;另一方面由于低压组分之间的相对挥发度变大,容易分离,所以与常压塔相比,减压蒸馏塔的塔板数减少了。
减压塔底部温度一般在390℃左右,如果停留时间太长,减压渣油分解和缩合反应会显著增加,塔的真空度下降,底部结焦。为此,减压塔底部采用减小塔直径。
此外,各种减压蒸馏馏分之间比较容易分离和分离精度要求不高,与塔的顶部不出一种产品,所以中间循环回流取热多、减压蒸馏塔的上部气相负荷小,可以缩径。
根据项目总体规划,常减压蒸馏的工艺流程在满足加氢裂化装置原料的基础上,一般多采用外甩一部分常压重油作为渣油加氢处理装置原料的方案,以减少减压蒸馏的加工负荷;再通过采用减压蒸馏技术,提高原油的切割温度,以达到降低减压渣油收率、得到更劣质的焦化原料、改善渣油加氢处理装置原料质量的目的。该方案的基本流程见下图。
1、流程特点
在常减压蒸馏的一般流程中,常压蒸馏部分主要完成原油中石脑油、煤油、柴油馏分的分离,外甩一部分常压重油减少了减压蒸馏部分的加工负荷,达到降低投资和节省能耗的目的。减压蒸馏的主要目的有两个:
①生产加氢裂化原料,通过调整轻、重蜡油的分离精度和减压蒸馏部分的加工量,满足加氢裂化装置原料的质量和数量要求。
②生产焦化原料,减压渣油一部分作焦化原料,一部分作渣油加氢处理装置的原料,通过调整减压蒸馏的拔出深度来调节焦化原料的质量,提高减压蒸馏拔出深度可以达到生产更劣质的焦化原料、改善渣油加氢处理装置原料的目的。
2、流程的不足
常减压蒸馏的设计思路是恰如其分地分离原油,根据原油性质,在满足全厂总体加工方案、装置配置和产品质量要求的前提下,采用恰当的流程,把原油分离成满足后续生产装置需要的各种馏分。前述原油常减压蒸馏一般流程存在着如下不足:
①常压重油外甩尽管可以减少减压蒸馏部分的加工负荷,达到降低投资和减少能量消耗的目的,但是会损失一部分直馏柴油。在装置生产运行时,常压重油中会溶解一部分柴油馏分,一般情况可达到8%左右,这部分柴油随着常压重油作为渣油加氢处理原料,经过催化裂化和产品精制,Z终成为商品。显然,该部分柴油的加工消耗了渣油加氢处理装置和催化裂化装置的能力和相应的能耗。
②为了得到劣质化的减压渣油作焦化装置的原料,以改善渣油加氢处理装置原料的质量,一般流程中减压蒸馏采用减压蒸馏技术提高原油的切割温度,造成了没有做焦化原料的那部分减压渣油被过分深拔,相当于一部分原油切割温度在520℃(TBP)左右的渣油,深拔之后又兑了回去,造成设备投资的增加和能量的浪费。
为了解决上述问题,采用两段减压蒸馏技术,满足目标产品的质量和数量要求,同时实现恰当地分离原油,达到常减压蒸馏装置投资和能量消耗的Z小化。两段减压蒸馏的基本流程见下图。
与常减压蒸馏的一般流程相比,两段减压蒸馏技术的流程主要特点如下:
①取消了外甩常压重油流程,可以使原油中的柴油组分得以全部回收;
②diyi段减压蒸馏的目的是生产加氢裂化原料,切割点在510℃左右,产品质量很好,操作条件也较为缓和,可以采用干式减压蒸馏技术,有利于装置节能;
③第二段减压蒸馏的目的是生产焦化原料,采用减压蒸馏技术,可以根据焦化装置的技术和生产情况灵活调节拔出深度和第二段减压蒸馏的进料量,以满足焦化装置的生产需要,实现生产劣质焦化原料,改善渣油加氢处理装置原料质量的意图。
在两段减压蒸馏技术流程中,diyi段减压蒸馏的减压渣油除作为第二段减压蒸馏的原料外,剩余渣油经换热后直接送出装置作渣油加氢处理装置的原料,不存在渣油加氢处理原料被过分蒸馏又兑回去的现象。
避免了由此带来的设备投资的增加和加工能耗的浪费。第二段减压蒸馏塔内可根据具体项目情况,仅设置2~3段填料,全塔压力降可以达到800 Pa以下,有利于减压蒸馏。第二段减压蒸馏塔仅设置2个侧线抽出(包括过汽化油),作为渣油加氢处理原料,可以在适当的位置并入渣油加氢处理原料参与换热,流程简单。
两段减压蒸馏技术的减压塔顶抽真空系统采用‘2-1-1’形式,即减顶一级抽空系统设置两组并联,分别用于一段和二段减压塔顶抽真空,两路塔顶气体在经过一级抽空系统后混合,之后依次进入减顶二、三级抽空系统,实现两点抽真空技术,简化了抽真空流程和投资。
与常减压蒸馏一般流程相比,两段减压蒸馏技术仅增加了一台减压蒸馏加热炉、一座设有2~3段填料床层的减压塔和5~7台机泵,diyi段减压蒸馏的减压塔和减压加热炉的规格尺寸也较一般流程减压蒸馏塔和减压加热炉的尺寸明显减小。
①本文由仪器网入驻的作者或注册的会员撰写并发布,观点仅代表作者本人,不代表仪器网立场。若内容侵犯到您的合法权益,请及时告诉,我们立即通知作者,并马上删除。
②凡本网注明"来源:仪器网"的所有作品,版权均属于仪器网,转载时须经本网同意,并请注明仪器网(www.yiqi.com)。
③本网转载并注明来源的作品,目的在于传递更多信息,并不代表本网赞同其观点或证实其内容的真实性,不承担此类作品侵权行为的直接责任及连带责任。其他媒体、网站或个人从本网转载时,必须保留本网注明的作品来源,并自负版权等法律责任。
④若本站内容侵犯到您的合法权益,请及时告诉,我们马上修改或删除。邮箱:hezou_yiqi