-
表界面 表面磷化处理
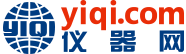
化学处理作为重要的表面处理技术广泛应用于金属防腐、涂装前处理、表面润滑以及表面精饰等领域。常用的化学处理方法有氧化、钝化、磷化3种。
磷化即金属铁、锌、铝及其合金在酸性磷酸盐溶液中进行化学反应,形成非金属或非导体转化膜的一个过程,这种转化膜的作用:①用于金属表层的预调整,方便金属成型加工;②用于金属表面的预处理,以便涂装,且可以防止涂层下的腐蚀;③提高防腐性能,为蜡和防锈油提供良好的底层;④用于金属表层的预处理,以便喷塑。
迄今为止,磷化层应用Z广泛的是作为涂装底层以及和各种涂料的配合使用,以延长涂层的使用寿命。此外,磷化处理技术在涂装行业起着巨大的推动作用。
传统磷化工艺迄今已有近140年的历史,磷化在整个金属表面处理中起着关键作用。英国人Coslett于1906年申请了diyi个铁盐磷化ZL,将铁屑溶于磷酸中制得磷化剂。接着,又有了锰系和锌系磷化等。
我国的磷化技术起步较晚,但经过多年的发展与不懈努力,在磷化技术的配方、工作机理等方面亦取得了较大进展,但技术含量较高、难度较大的表面处理技术仍然采用国际产品。
有学者对品粒细化剂的研究表明:加入钦盐进行表面调整,可加快磷化速度,减少磷化时间,对晶粒的细化有一定作用。重金属离子加入到磷化液本体后,可提供磷化过程的成核结晶点,可提高磷化速度并细化晶粒,
有学者的研究表明:磷化时间达到30s时,浸蚀后暴露出了原始组织中的缺陷和无定形沉淀。延长磷化时间,无定形沉淀加倍增加,进而形成膜层。
有学者的实验结果表明:磷化膜结晶形貌中锌的含量是有影响的,发现低锌含量磷化膜的形态并不具有像针一样的精细结构,而是球状或颗粒状结构。
磷化处理材料的主要成分为磷酸二氢盐(锌、锰、铁等金属),磷化过程通常在磷酸二氢盐的水溶液中进行。磷酸二氢盐的水溶液发生水解,将产生游离磷酸:
3Me(H2PO4)2=Me3(PO4)2+4H3PO4
游离磷酸同被磷化金属表面的金属反应,并放出氢气,以钢铁为例,反应为:
Fe+2H3PO4=Fe(H2PO4)2+H2↑
反应释放出来的氢气被吸附在金属表面,从而阻止磷化膜结晶的形成。为加快反应速度,磷化液中一般都要加入氧化剂和催化剂以去除氢气。以亚硝酸钠为催化剂为例,亚硝酸盐分解产生NO2,NO2可使金属表面的氢气氧化生成水,同时将部分亚铁离子Fe2+氧化为Fe3+,铁离子和磷酸根反应生成FePO4瘀渣沉淀,反应为:
Fe+H2PO4+NO2=FePO4+H2O+NO↑
上述反应降低了溶液的酸度,当PO43-与溶液中的金属离子(Zn2+、Mn2+、Ca2+、Fe2+等)的浓度达到溶度积常数时,就会在金属表面形成磷酸盐沉淀,即磷化膜,反应式为:
3Fe2++2PO43-→Fe3(PO4)2↓
随着金属表面上磷酸盐的沉淀,磷化反应也随之减慢,当整个表面被磷化膜全部覆盖后,磷化过程结束。磷化瘀渣的主要成分FePO4,磷化膜的主要成分是Me3(PO4)2、H2O,也有少量的氧化铁和FePO4。
1、按磷化膜种类
按磷化膜可分为锌系、锰系、铁系、锌钙系、锌锰系、非晶相铁系。各种磷化膜的主要成分见下表。
2、按磷化膜质量
根据单位面积膜层质量(g/m2)可分为重量级、次重量级、轻量级、次轻量级4种。通常膜薄附着力好,而膜厚耐蚀性好。涂装前处理所需膜层为0.5-7.5g/m2,一般锌系磷化膜控制为1~4.5g/m2,铁系磷化膜控制为0.2~1g/m2,与粉末涂料配套时磷化膜控制为1~3g/m2。
3、按磷化处理温度
①高温磷化
磷化处理温度为80~90℃。优点是配方简单,磷化速度快,磷化膜的耐蚀性、硬度及耐热性较高。缺点是能耗大,沉渣多,成本高,且磷化膜较厚且粗糙,一般不作为涂装前的磷化。
②中温磷化
磷化处理温度为50~75℃。优点磷化速度较快,磷化膜的结晶较细、耐蚀性性好。但磷化膜仍较厚,涂装后光泽不好,一般适用于耐蚀性防护层及喷、刷漆的底层。
③低温磷化
磷化处理温度为35~55℃。低温磷化成膜的动力主要依靠促进剂,形成的磷化膜薄而致密,光滑平整,综合成本较低,是目前涂装底层处理的主要技术。
④按磷化工艺
可分为浸渍法、喷淋法、涂刷法。
一般情况下,磷化处理要求工件表面应是洁净的金属表面(二合一、三合一、四合一例外)。工件在磷化前必须进行除油脂、锈蚀物、氧化皮以及表面调整等预处理。特别是涂漆前打底用磷化还要求作表面调整,使金属表面具备一定的“活性”,才能获得均匀、细致、密实的磷化膜,达到提高漆膜附着力和耐腐蚀性的要求。因此,磷化前处理是获得高质量磷化膜的基础。
1、脱脂
除油脂的目的在于清除掉工件表面的油脂、油污。包括机械法、化学法两类。机械法主要有手工擦刷、喷砂抛丸、火焰灼烧等。化学法主要有溶剂清洗、酸性清洗剂清洗、强碱液清洗、低碱性清洗剂清洗。应用较为广泛的是碱液除油。
2、除锈、除氧化皮
各种除锈方法中,酸洗除锈是应用Z为广泛的方法。酸洗中使用Z为常见的是盐酸、硫酸、磷酸。盐酸酸洗不宜超过45 ℃,使用浓度为10%~45%。硫酸适合的温度为50~80 ℃,使用浓度为10%~25%。如果硫酸中含有砷时,应加入 0.1~0.2 g/L硫代硫酸钠将砷去除。磷酸酸洗一般使用浓度为10%~40%,处理温度可从常温到80 ℃,不会产生Cl-、SO42-腐蚀性残留物,但成本较高,酸洗速度较慢。也可采用盐酸-硫酸混合酸、磷酸-柠檬酸混合酸。
3、水洗
在磷化工艺中,脱脂后和除锈后需进行水洗以除去附着在工件表面的活性剂和各种离子。将清洗后水的pH值控制在6.0~8.0之间,可以有效YZ各种离子对后续磷化的不利影响,必要时可以采用多级水洗。
4、表面调整
表面调整是指采用机械或化学等手段,使金属表面改变微观状态,增加磷化晶核的数量,使工件表面活性均一化,进而形成细致密实的磷化膜,以及提高磷化速度。一般采用强碱性脱脂剂、进行酸洗的工件都应进行表面调整。表面调整剂主要有两类,一类是含有草酸的表调剂,主要由草酸、表面活性剂、络合剂等组成;另一类是含有胶体钛的表调剂。
1、磷化液的组成
磷化液的主要组成部分为开槽剂和补充剂。开槽剂仅在diyi次建槽时使用。补充剂用于建槽后的补充需要。磷化促进剂作为氧化剂,起着去极化作用,可加快磷化反应速度,促进磷化膜的形成。磷化表而调整剂主要是调节磷化液的总酸度和游离酸度,以获得合适的酸比。
2、磷化液的使用方法
将待处理工件放入脱脂液中,水洗后放入酸洗处理液中。可完成零件表面除油除锈的基本要求。油锈除净后方可取出放入流水池中再次进行水洗。水洗取出后再浸入磷化液中,浸泡后取出自然晾干或风干即可。取出的磷化钝化件,放置一段时间,便可观察到处理工件表面会产生一层均匀、致密的磷化膜。磷化主要工艺流程如下:
预脱脂→脱脂→水洗→除锈→水洗→表面调整(根据磷化膜体系的不同可能无此道工序)→磷化(以便成膜)→水洗→涂装处理(如电泳或粉末涂装)
1、磷化液成份的作用
磷酸:提供H+,调节处理液的酸度,游离酸度对加快磷化速度,促使磷化膜致密起着重要作用。游离的磷酸含量越高,游离酸度越高,酸比越低。同时它在溶液中会离解为H2PO42-和PO43-等阴离子,这此离子在磷化液中的浓度随pH值不同时的分布系数而定。
铝盐:提供Al3+,与溶液中的PO43-反应,会沉积在钢铁表面,形成致密的膜另外,从铁表面溶解出的Fe2+也与PO43-反应,形成Fe3(PO4)2膜。这些磷化膜可保护铁基,防止铁基被氧化腐蚀。
表面活性剂:降低液体表而张力,使溶液润湿,对金属表面粘附的油渍具有乳化、增溶的作用,且能阻止油粒再次吸附在金属表面。
缓蚀剂:有机缓蚀剂的加入,一方面可减缓金属铁在酸性溶液中的氧化,这是因为缓蚀剂分子中带极性基的一端被金属表面所吸附而使分子疏水的一端向上排列,结果就使得介质被缓蚀剂的分子排挤出来,将介质与金属表面隔离开来,从而大大降低了金属的被腐蚀程度。另一方面,缓蚀剂吸附在钢铁表面微电池阴极区域,增加了阴极极化,使析氢反应更加困难,减缓铁基的溶解速度。但对于酸与金属氧化物,缓蚀剂的作用并不明显,缓蚀剂的加入对介质的除锈影响不大。
2、酸度对处理效果的影响
①总酸度
总酸度是检测磷化液浓度高低的一项重要标准,对磷化有很大的影响。控制好总酸度,必须控制好成膜离子的浓度,使之保持在合适的范围内。总酸度偏高,膜层粗糙、疏松、附着力差,表面有浮灰;总酸度偏低,则膜薄甚至不成膜、总之,过高、过低的总酸度均对成膜不利,控制在合适范围内Z好。
②游离酸度
游离酸度是磷化液中游离H+含量的一个重要指标,偏高或者偏低均会对磷化成膜有一定的影响。过高,不能成膜,易出现黄色斑迹;过低,会影响磷化液的稳定性,产生副反应;控制游离酸度,其实就是控制磷酸二氢盐的离解度,控制成膜离子的浓度在使用过程中,磷化液的游离酸度会自然缓慢升高,此时可用碱来中和。此外,值得注意的是,游离酸度与总酸度单一看来是没有什么根据可寻的,必须结合在一起来看。
③酸比
酸比指的是总酸度与游离酸度的比值。换言之,即酸比随总酸度的增加而增加。酸比小的配方,生成磷化膜的速度慢,磷化时成膜时间长,其游离酸度比较高,处理时所需温度也较高;反之,磷化时成膜时间短、所需处理温度低,生成膜速度较快。通常酸比控制在5-40之问比较合适。
3、温度对处理效果的影响
磷化处理温度是成膜的另一重要控制因素。因配方差异,处理的温度亦不同。高温时,磷酸二氢盐的离解速度快,会相应提高成膜离子浓度;但是温度过高,会导致副反应的发生,亦会产生大量磷化沉渣,使得磷化液失去原有平衡;温度过低,成膜离子达不到所需浓度,则不能生成完整、致密的磷化膜。总之,温度要适宜。
4、时间对处理温度的影响
因各个配方不同,规定的工艺时间也就不同。时间过短,所需成膜量不够,难以形成致密、附着力好的磷化膜;时间过长,可能导致磷化膜表面粗糙、疏松。
如今,提高磷化质量,减少环境污染,节约能源是磷化技术领域的ZD研究方向。磷化处理中产生的污染源主要是磷酸盐、重金属、有毒物质等。基于环保的要求,今后磷化技术的发展方向主要趋向于以下三方面:
①成膜物质浓度的转变。磷化处理中的污染源主要是成膜物质锌离子、磷酸盐等。由于现有技术的局限性,取代磷酸盐是不可能的。已有的不含锌的磷化技术,其磷化质量远比不上锌磷化。听以若能将成膜物质的浓度由高浓度转向低浓度,不仅可以降低成本,减少沉渣,而且可以起到减轻污染的作用。
②致癌物的替代。亚硝酸盐虽然是很好的促进剂,但它却含有致癌物,严重威胁人类健康,人们正在寻找其他物质来替代它。在这方面可以使用双氧水、羟基化合物、稀土类助剂等,取代亚硝酸盐是历史必然。
③节约能耗。磷化过程是一系列的反应过程,不管是物理还是化学反应均需要一定的温度,而温度能耗较大。所以磷化技术发展的趋势是向低温方向转变;另外,还需强调磷化工艺过程的简单化。
总之,磷化处理正朝着低成本、低能耗、低毒、无污染、磷化膜均匀致密、膜薄且耐蚀性能好的方向发展。
①本文由仪器网入驻的作者或注册的会员撰写并发布,观点仅代表作者本人,不代表仪器网立场。若内容侵犯到您的合法权益,请及时告诉,我们立即通知作者,并马上删除。
②凡本网注明"来源:仪器网"的所有作品,版权均属于仪器网,转载时须经本网同意,并请注明仪器网(www.yiqi.com)。
③本网转载并注明来源的作品,目的在于传递更多信息,并不代表本网赞同其观点或证实其内容的真实性,不承担此类作品侵权行为的直接责任及连带责任。其他媒体、网站或个人从本网转载时,必须保留本网注明的作品来源,并自负版权等法律责任。
④若本站内容侵犯到您的合法权益,请及时告诉,我们马上修改或删除。邮箱:hezou_yiqi