-
工业处理技术 热处理
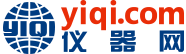
热处理的发展历史可以追溯到公元前770至222年,那时我们的祖先就依靠自己的聪明才智和实践经验,开拓出了独特的热处理发展之路。通过将钢铁在不同的温度加压变形处理后,可以得到所需的物理化学性能。
例如,人类在很早以前就会通过陨铁这种高铁镍合金,采用退火或热锻加工,来制造所需的小件物品。在河南洛阳出土的铁铲和空首铁锄,据分析大约是在经过900℃或稍高的温度下,进行长时间的退火,才得到了完善的组织和性能。正是退火这一纯熟的热处理工艺,使得铁器能够大规模应用和推广。
现代热处理技术理论的发展起源于1868年,俄国冶金学家D.K切尔诺夫在实验中发现加热和冷却钢的过程中有组织转变。后来FI奥斯蒙德用热分析的方法,确定了钢相变的临界点温度,并建立了合金状态图,为钢的热处理提供了Z初的理论依据。后又经过F.C贝茵、P.梅拉、P德拜、G.V库久莫夫和萨克斯等科学家对相变机制进行了系统的研究,解释了金属热处理过程中强度和韧性变化的机理。
在热处理的生产装备上,各个国家相继开发了井式炉、盐浴炉、可控气氛炉、渗碳炉、渗氮炉等,为新式的热处理技术的进步提供了广阔的前景。
随着工业现代化生产的发展,制造技术的关键更多地在于工业生产的优质、GX、低耗、环保和产品竞争能力提高。冶炼流程中,技术的提高可以保证金属的成分,而成分确定后,却不能保证其具有足够的性能,此时就需要通过热处理来改善。
不同的热处理流程,能够让金属根据需要,强化金属材料的性能,挖掘材料的潜力,降低结构重量,节省材料和能源。热处理过程并不需要改变金属整体的化学成分,节省了加工时间,赋予零件所需的特殊性能。热处理能提高产品质量,保证生产GX、节能,符合当下工业现代化的要求。
热处理在金属的应用推广中起到了极为关键的作用。钢铁在铸、锻、焊等热加工后存在的各种缺陷,均可以通过合适的热处理过程消除,例如细化晶粒、消除偏析、降低内应力、增强抗磨损、耐腐蚀等特殊的物理化学性能。
如特钢厂热轧后的合金钢型材要进行热处理,汽车制造中70%~80%的零件需要热处理。钳工用的錾子经过热处理,变得锋利而韧性,用锤子经常敲打也不易发生卷刃和崩裂。热处理为金属材料的加工和Z终的应用提供了必要的条件。
热处理是将金属在固态下加热到预定的温度,保温一段时间,然后以一定的速度冷却到室温。在整个冷、热加工工艺中穿插多次热处理工艺,充分发挥金属的潜力。其中,影响组织和性能的关键因素在于加热速率、加热温度、保温时间和冷却速度。
各因素变化的搭配将热处理工艺分为退火、正火、淬火、回火、表面淬火以及化学热处理等。由于要达到的目的不同,因此采取的工艺不同。为了随后的机械加工或进一步热处理作好组织准备,称为预备热处理,通常为退火或正火;直接赋予工件所需要的使用性能的热处理,称为Z终热处理,通常为淬火和回火。
各种钢由于其成分和用途不同,因而要采取不同的热处理工艺。工艺的具体流程和原理理解比较复杂,以轴承钢的热处理为例,结合做菜的日常知识帮助理解热处理的效果。
将轴承钢放入炉子内加热,等待一段时间升温到指定的温度,一般为850℃左右,并在一定时间内保温,约为4~6h后轴承钢在炉子里和加热炉一起缓慢降温,到室温后出炉。这个时候,轴承钢才能“熟透”变软,成分变得均匀,近于平衡组织。钢的软,体现在其硬度下降,容易加工。此时我们可以根据使用的需要,通过车、铣以及压缩或拉伸等加工工序,加工成各种形状服役使用。
退火可以消除铸件、锻件及焊接件的内应力及成分和组织的不均匀性,改善和调整钢的力学性能和工艺性能,为接下来的工序做好组织性能准备。退火效果类似烹饪中的“煮”,时间越长,各种佐料味道的均匀性越好,而对于钢而言则是成分越均匀。对于受力小、性能要求较低的机械零件,退火或正火可以作为Z终的热处理。
钢的退火热处理原理基于钢在不同的温度和冷速下组织性能不同。在高温下长时间保温,一般为727℃以上,会出现奥氏体显微组织。
奥氏体组织为碳溶于γ-Fe中的固溶体,塑性很好,强度较低,具有一定的韧性,有顺磁性。因此,钢在加热到高温时,较容易变形,可以进行热轧等工艺。从高温下缓慢冷却,从奥氏体中析出渗碳体,其余组织为铁素体。渗碳体是铁和碳形成的化合物,含碳量很高,具有很高的硬度,但塑性很差,塑性、冲击韧性和伸长率几乎等于零,脆性极大。
铁素体是碳溶于α-Fe中的间隙固溶体,溶解的碳量比奥氏体小,具有良好的塑性和韧性,但强度和硬度都很低,伸长率高。退火经过缓慢冷却得到渗碳体和铁素体的混合物,含量比值为1∶8,称为珠光体。由于铁素体含量高,因而珠光体总体性能表现较软,退火后可以为加工做好准备。
淬火工艺与退火类似,但其ZD在于保温温度较高,冷速较快。先给加热炉升温,一般在900℃及以上,然后将轴承钢放入炉内,等钢件达到指定温度后,在较短时间内保温,约30min。钢件出炉直接放入机械油或水中淬火,由于其加热温度高,放入油或水中冷却速度快,等待温度降到170℃左右拿出空冷至室温。高温短时间保温,并快速降温,钢变得硬起来,伴随着钢的强度和硬度升高,韧性有所下降,变得“酥脆”了。
淬火可以显著提高钢的强度、硬度、耐磨性,结合回火工艺,可以得到强韧结合的优良综合力学性能,还可以提高弹簧钢的弹性极限。其目的类似油炸或烧烤土豆片,利用短时间内高温加热,快速降温,得到Z终高硬度、高强度,“酥脆”性能。淬火工艺是热处理强化的重要手段之一,配合回火工艺,可以达到钢件所需的Z终使用性能。
淬火的原理也是基于钢在不同温度加热和不同冷速下冷却,组织不同,导致性能不同。在高温下,同退火状态相似,但其温度较高,钢中组织全为奥氏体,奥氏体软而韧。为得到一定的硬度,要快速降温,以大于临界淬火速度冷却,渗碳体来不及从奥氏体中析出,以得到大量的马氏体组织。
马氏体与原奥氏体的成分基本相同,区别在于,其结构发生变化,属于碳在α-Fe中的固溶体,但固溶量要比铁素体多,是碳的过饱和状态。碳含量在一定范围内越高,马氏体硬度和强度就越高,同时韧性变差,硬而脆,可塑性差。钢中马氏体越多,则钢的强度和硬度越高,可以按照服役需要改变工艺,调配马氏体含量。
淬火工艺在现代机械制造工业得到广泛的应用。机械中重要零件,尤其在汽车、飞机、火箭中应用的钢件几乎都经过淬火处理。
钢经过淬火以后,得到的马氏体,属于碳的过饱和状态,且淬火后保留有一定的待转变奥氏体,在室温下处于亚稳定状态,都趋于向铁素体和渗碳体的稳定状态转化。回火恰是通过升温来促进这种转化,可以有效地防止淬火后钢的变形和开裂,并获得稳定的组织和所需的性能。
其过程类似将油炸薯片再次加热,这个过程必然导致薯片失去原来脆的口感,出现一定的韧性,硬度有所降低。此时可以通过控制回火的温度和时间,来协调钢的强度硬度和韧性之间的关系。对于高温轴承钢来说,在500℃左右加热,保温2h,出炉空冷至室温,反复三次。此时可以保证亚稳态的马氏体和残余奥氏体发生转化,碳化物从马氏体中大量析出。
碳的减少导致马氏体的塑性和韧性提高,析出的碳化物可以弥补硬度值的降低,从而同时具备高强度、高硬度和一定的韧性,从而达到轴承钢Z终所需要的理想性能。
回火工艺是轴承钢的Z终热处理,足够的硬度能保证其具有足够的耐磨性和疲劳强度,在服役中不至发生破裂,一定的韧性可以防止裂纹的出现和扩展,提高服役寿命。
近年来我国的热处理工艺的到了迅速的发展,其新发展的热工艺与技术其不仅具备有更高的准确性以及有效性,并且能够使得该金属材料的质量以及整体应用性能得到进一步的提升。
1、化学处理薄层渗透工艺
化学处理薄层渗透技术其主要是对金属材料进行了化学处理,并能够通过化学热处理的方式来完成金属材料的薄层渗透工作,从而使得该金属材料的坚韧性得到更进一步的提升。此外通过化学处理薄层渗透技术,其能够Z大限度的降低金属材料的浪费,并能够有效避免对于环境的污染,从而取得良好的经济效益以及环保效益。
在对金属材料进行化学热处理的过程中,其只需要渗透到金属薄层,就能够使得该金属材料的性能得到有效的提升,这样也就使得金属材料的处理效率得到提升。
2、激光热处理工艺
激光具备有非常强的穿透性,因此对于一些表面比较坚硬的金属材料进行热处理的过程中,也就可以通过激光技术来完成这项工作,并能够取得良好的金属材料热处理效果。
通过激光热处理技术在金属材料处理过程中的应用,其能够使得金属表面的硬度得到一定程度的增加,而为了使得激光热处理的工作效率得到进一步增加,也就需要通过计算机来实现相应的控制效果,并借此来实现激光的热处理自动化发展。
3、超硬涂层工艺
该热处理技术主要进行的是金属材料的表层处理,并不会对该金属材料的内部进行任何处理,而在现有的金属材料热处理技术中,超硬涂层技术也是应用Z为广泛的一种金属材料热处理技术。
采用超硬涂层技术其能够在完成金属材料的热处理这一过程中,来让该金属材料的表面硬度得到有效的提升,并能够使得该金属材料做制成的成品变得更加的耐用。此外超硬涂层技术其还能够使得金属材料的使用性能得到显著的提升,并拥有者快捷方便的应用优势。
4、热处理CAD工艺
热处理CAD技术作为现阶段金属热处理技术中的一种先进技术,其主要是借助于计算机技术先进行热处理工艺的模拟,然后再借助于智能处理的方式来实现金属材料的热处理。
在对金属材料通过CAD技术来进行热处理时,其首先需要工作人员在计算机上面进行该热处理CAD技术的模拟还原,然后在此基础上结合相应的热处理过程来进行热处理测量的针对性制定,从而完善该金属材料的处理环节。
在金属材料的热处理过程中通过CAD技术的合理应用,因此存在有模拟处理步骤,所以能够对该金属材料的热处理效果进行有效的预见,能够及时发现热处理过程中所存在的问题并加以改正,这样就可以有效避免一些金属材料热处理过程中出现的不必要问题,并使得该金属材料的性能得到一定程度的提升。
5、真空热处理工艺
真空热处理技术其指的是借助于真空来完成相应的金属热处理工作,借助于真空热处理技术来进行金属材料的处理过程中,其具备有效率高的特点,并且能够对加工过程中所产生的各种有毒废气进行有效的控制,因此说真空热处理基础其能够使得金属热处理工作的工作效率得到更进一步的提升,并且能够取得一个良好的环境保护效果。
6、振动时效处理工艺
在通过振动时效处理技术来完成金属材料的热处理工作时,其能够直接借助于振动来完成金属材料材料的热处理工作,并能够使得该金属材料的稳定性得到进一步的提升。此外该热处理技术还不会使得该金属材料的性状产生变化。
在通过振动时效处理技术来进行金属材料的处理过程中,其往往需要借助于现代的计算机技术来进行热处理工艺的监督以及控制工作,并借此来实现振动时效热处理的自动化控制,并使得相关金属制品的生产时间得到明显缩短,来使得该企业的生产效益也得到有效的提升。
真空热处理设备始于20世纪20年代,但是其真正发展还是从20世纪六七十年代开始的,主要是因当时市场的需求及材料的研究发展。
真空热处理的工作环境其实是指低于一个标准大气压(1.013×105Pa),包括低真空(105~102Pa)、中真空(102~10-1Pa)、高真空(10-1~10-5Pa)、超高真空(<10-5Pa)。
真空热处理相对来说也是可控气氛热处理,只是其工作环境空气极其稀薄,工件在真空状态加热可以避免常规普通热处理的氧化、脱碳,避免氢脆,变形量相对较小,提高材料零部件的综合力学性能。经真空热处理后的部件寿命通常是普通热处理的寿命的几十倍,甚至几百倍。
1、真空加热的特点
材料在传热过程中主要是有三种方式:传导、对流、辐射。
而真空状态下的加热环境是极其稀薄的气氛,所以部件加热不存在氧化脱碳的现象,同时它的传热方式也只有单一的辐射,辐射热量的大小与温度成四次方的正比:E=C(T/100)4,故真空加热速度慢,但因几乎没有什么热损失,发热体升温很快,工件表面与心部温差不是很大,相对来说,工件变形量也较小。
同时我们从式中分析到,在真空阶段内,靠辐射一种传热方式加热,低温辐射效果较差,在高温阶段辐射效果较好。该现象在后面的工艺参数制定时将会用到。
2、真空度的选择
材料在真空热处理时,要考虑到真空度的合理性。合金元素Mn、Ni、Cr等合金元素在真空状态加热会挥发,挥发物会使工件粘结在料筐丝网上,不便取出;还有挥发物会污染真空系统如加热室、真空泵,所以在启动加热时,要注意各种金属的蒸气压,在许可的情况下Z好通入1~2kPa高纯氮气。其目的,一是为了减小合金元素的挥发;二是为了提高真空加热速度,减小真空加热滞后时间。
在真空加热的环境下,工作真空度的选择原则是:低温用高真空,高温用低真空,我们在真空度上的取决不仅是工件还要取决于设备使用寿命,因为真空设备加热系统目前大多是石墨的,真空度不够将降低石墨的寿命,成本会增加很多。
对于大部分低合金金钢、高铬钢来说,真空加热一般情况下可以选择1.33-13.3Pa;可是像高碳高合金钢高温回火时,真空度要选择在1.33×10-2Pa;碳素钢在真空加热时,真空度不能低于1.33×102Pa;对于在高温高真空条件下加热时,如含钛、含钨等材料它们的加热温度差不多在1250℃,真空度也要控制在1.33×10-2Pa左右,为防止部分元素挥发及工件粘结,高温时要加一点高纯氮,提高炉压。其实在起始加热时,真空度Z低也要达到6.67×10-1Pa时方可升温。
1、研发高端热处理设备
(1)绿色高端热处理设备
高端热处理设备的Z大特点就是绿色化,即在整个热处理过程中不会对环境造成负面影响,在符合国家倡导的可持续发展前提下实现优质处理的目标。
热处理设备的工作环境非常的恶劣,极高温和极低温的情况时常出现,运行时操作的精度又非常高,所以要想实现热处理绿色化的要求,技术人员必须要ZD关注热处理设备和能耗和排放问题,通过科学的系统设计来保持热处理设备的较高性能。经济化趋势和“一带一路”是我国发展绿色高端热处理设备转型升级的重大历史机遇。
(2)智能高端热处理设备
智能高端热处理设备的研发是建设智能化工厂的基本前提,智能化不仅对热处理设备自动化的要求比较高,而且还对其在线热处理处理工艺设计提出了更高的要求。
智能化高端热处理设备的采集系统和控制系统的智能化水平都非常高。在工业物联网迅速发展的前提下,智能高端热处理设备还需ZD发展信息化,能具备自我检测和诊断等功能。此外,智能高端热处理设备还需满足车间技术要求、生产线技术要求以及车间管信息化技术要求等等。
(3)可靠高端热处理设备
以前我国热处理设备的主要缺点就是可靠性比较低,要想让我国热处理技术走出国门,就必须要提高热处理设备的可靠性。热处理设备在运行时的可靠性指的是装备的密封性以及炉压的保持程度等指标,任何一个参数不满足要求都会给热处理过程造成极大的影响。我国对可靠高端热处理设备的主要标准是有以下几方面:
①在一年之内不能因为设备的设计和制造原因而在正常运行中出现降低检修的问题。
②在半年内不能出现因为设备设计和制造原因出现能迅速修复不影响正常运行的故障。
③在一个月内不能出现设备元件质量问题和安装不牢固等问题。
以上三点是可靠高端热处理设备的主要标准,其余对材料和元件等的标准还有很多,这些标准共同构成了可靠高端热处理设备质量的重要保障。
2、研发绿色清洁的热处理技术
(1)真空高压气淬技术
真空高压气淬技术中的油淬和水淬不会散发出有毒的污染物质,而且也不会排放出含油废液,比如二氧化碳和二氧化硫等物质更不会排放出来。应用真空高压气淬技术的工件能保持非常高的清洁度,不用再进行后续清洗工序。高合金钢和模具钢是应用真空高压气淬技术的主要材料。
(2)真空低压渗碳技术
真空低压渗碳技术不需要一氧化碳和二氧化碳,所以它能够成为可控气氛渗碳的替代品。真空低压渗碳技术可以提高碳转移的GX性,极大节省了渗碳所需的时间,并显著减少了污染物的排放。渗碳零件表面的清洁度很高,能防止出现晶间氧化的现象。低碳马氏体不锈钢和微合金钢比较适合应用这种技术,大批量或小批量生产都可实现。
(3)余热利用热处理技术
应用余热利用热处理技术能在一条作业线上实现锻造和淬火以及回火等工序,极大缩短了生产时间,有效降低了生产成本。锻造淬火比普通热处理技术的力学性能有了显著提高。
3、关键部件的热处理
关键部件的热处理效果直接关系着整个机械的性能和精度,所以,技术人员一定要对关键部件的热处理工艺给予足够的重视。
①热处理生产企业应该重视材料的冶金质量,反复确认核心材料的质量,认真检查材料的生产合格证和质量检测报告。
②不断对热处理工艺进行创新,尤其是对真空低压渗碳和高压气淬技术工艺进行创新。
③制定出完善的热处理技术规范,为严把热处理生产质量关提供重要保障。
①本文由仪器网入驻的作者或注册的会员撰写并发布,观点仅代表作者本人,不代表仪器网立场。若内容侵犯到您的合法权益,请及时告诉,我们立即通知作者,并马上删除。
②凡本网注明"来源:仪器网"的所有作品,版权均属于仪器网,转载时须经本网同意,并请注明仪器网(www.yiqi.com)。
③本网转载并注明来源的作品,目的在于传递更多信息,并不代表本网赞同其观点或证实其内容的真实性,不承担此类作品侵权行为的直接责任及连带责任。其他媒体、网站或个人从本网转载时,必须保留本网注明的作品来源,并自负版权等法律责任。
④若本站内容侵犯到您的合法权益,请及时告诉,我们马上修改或删除。邮箱:hezou_yiqi