高低温湿热试验箱在材料、电子、航空航天等众多领域的产品质量检测与可靠性评估中发挥着关键作用。在实际使用过程中,试验箱内试样的放置数量常常会有所不同,而当试验箱放满试样时,其内部的热湿传递过程、气流分布以及设备的整体性能都可能发生变化,进而对测试结果产生显著影响。深入探究这些影响及其背后的原理,对于准确进行产品测试和评估具有极为重要的意义。
升温速率减缓:当试验箱内放满试样时,试样本身具有一定的热容量,需要吸收大量的热量才能升高温度。这就导致试验箱的加热系统在对环境升温时,不仅要加热箱内的空气,还要对众多试样进行加热。例如,在对一批金属材料试样进行高温测试时,相比于空载状态,满载时加热系统的热量被分散到更多的对象上,使得升温过程变得缓慢。原本在空载时能够在 30 分钟内从 25℃升温至 100℃的试验箱,在满载试样后,可能需要 60 分钟甚至更长时间才能达到相同的高温设定值,从而影响了测试的时间进程和效率。
降温延迟与不均匀性:在降温阶段,类似的情况也会发生。试样会阻碍热量的散发,试验箱的制冷系统需要克服试样的热阻来降低温度。而且由于试样的分布和热传导特性不同,可能会导致箱内不同位置的降温速率不一致。例如,靠近制冷蒸发器的试样可能降温较快,而位于中心或角落的试样降温则相对较慢。这种降温的延迟和不均匀性可能会使某些对温度变化敏感的试样在测试过程中经历不同的热历程,进而影响其测试结果的准确性和一致性。比如在电子元器件的低温测试中,不同位置的元器件可能因为降温差异而表现出不同的性能变化,导致测试数据的离散性增大。
加湿与除湿效率降低:在高低温湿热试验箱中,湿度的控制是通过加湿和除湿装置来实现的。当箱内放满试样时,试样的存在会干扰水汽的扩散和凝结过程。在加湿过程中,水汽需要在众多试样之间扩散才能达到均匀分布,这增加了加湿的难度和时间。例如,对于一些吸水性较强的试样,如木材或纸张类产品,它们会吸收大量的水分,使得箱内湿度难以快速提升到设定值,降低了加湿效率。相反,在除湿时,试样表面的水分蒸发也会影响除湿装置的正常工作,导致除湿速度变慢。如在对潮湿环境下的塑料产品进行测试时,满载试样可能会使箱内湿度长时间维持在较高水平,无法及时达到预期的低湿度设定,影响对塑料产品耐湿性的准确评估。
湿度分布不均:由于试样对水汽的吸附、释放以及对气流的阻挡作用,箱内湿度的分布均匀性也会受到破坏。不同位置的试样周围湿度可能存在较大差异,这种湿度差异可能导致同一批次的试样在测试过程中出现不同的性能变化。例如,在对纺织品进行耐湿热老化测试时,靠近加湿器出口处的纺织品可能因为湿度较高而更快地出现霉变或褪色现象,而远离加湿器的纺织品则可能变化相对较小,使得测试结果不能真实反映该批次纺织品在均匀湿热环境下的性能表现。
气流受阻与紊乱:试验箱内的气流组织对于保证箱内温度和湿度的均匀性至关重要。当放满试样时,试样会占据箱内的空间,阻碍气流的正常流动。原本设计的合理气流通道被破坏,气流可能会在试样之间形成漩涡或局部滞留,无法按照预定的路径循环。例如,在一些具有复杂形状试样的测试中,如航空航天零部件,这些零部件的不规则外形会严重干扰气流,使气流在通过时产生较大的压力损失和流向改变,导致箱内部分区域出现气流死角,这些死角区域的温度和湿度与其他区域存在明显差异,影响测试结果的可靠性。
传热传质不均匀性加剧:气流受阻和紊乱进一步加剧了传热传质的不均匀性。由于气流不能均匀地掠过每一个试样表面,试样与空气之间的热交换和湿交换变得不稳定且不均匀。这可能导致一些试样表面的温度和湿度与设定值偏差较大,而另一些试样则相对接近设定值。在对涂层材料进行高低温湿热循环测试时,不同位置的涂层可能因为所经历的实际热湿环境不同而出现不同程度的剥落、起泡等现象,使得对涂层材料的耐候性评估产生误差,无法准确判断其在实际使用环境中的性能表现。
制冷与加热系统负荷增大:试验箱内满载试样意味着设备的负载大幅增加,制冷系统和加热系统需要消耗更多的能量来维持设定的温度条件。长时间处于高负荷运行状态下,设备的制冷和加热元件容易出现疲劳和性能衰退。例如,压缩机可能会因为长时间连续工作而导致制冷效率下降,加热丝可能会因为频繁启停而出现局部过热、烧断等现象。这种设备性能的变化会直接影响测试结果的准确性和稳定性,如在对高精度电子仪器进行温度稳定性测试时,由于设备性能的波动,可能会使测试得到的仪器温度漂移数据出现偏差,无法准确评估仪器的质量可靠性。
风机性能与可靠性挑战:风机在试验箱内起着推动气流循环的关键作用。在试样满载的情况下,风机需要克服更大的阻力来维持气流的正常循环。这会增加风机的工作负荷,使其转速下降、风量减少,甚至可能导致风机故障。例如,当风机的风量不足时,箱内的温度和湿度均匀性将难以保证,而且风机故障可能会导致测试中断,影响测试的连续性和完整性。在一些长期的可靠性测试中,风机的不稳定工作可能会使测试结果出现异常波动,无法为产品的可靠性评估提供可靠的数据支持。
合理规划试样放置:根据试验箱的内部结构和气流组织特点,合理安排试样的放置位置和方式。尽量避免试样堆积在一起,保证气流能够在试样之间顺畅流通。可以采用分层、分区域放置的方法,同时在试样之间预留一定的间隙,以减小对气流的阻碍。例如,在对小型电子元件进行测试时,可以将元件放置在特制的托盘上,托盘之间保持适当的距离,使气流能够均匀地流过每个元件。
优化试验箱设计:在试验箱的设计阶段,充分考虑试样满载时的情况,优化气流通道的设计,增大风机的功率和风量,提高制冷和加热系统的容量和效率。例如,可以采用新型的风道结构,如分流式风道或环形风道,使气流能够更均匀地分布在箱内。同时,选用性能更优良的制冷和加热元件,如采用高效的涡旋式压缩机和陶瓷加热元件,以提高设备的整体性能和应对满载试样的能力。
增加辅助设备与监控手段:安装更多的温度和湿度传感器,对箱内不同位置的温湿度进行实时监控,以便及时发现温湿度不均匀的情况并采取相应措施。此外,可以配备辅助的气流调节装置,如导流板或风量调节阀,根据实际测试情况对气流进行动态调整。例如,当发现某个区域温度过高或过低时,可以通过调节导流板的角度来改变气流方向,使该区域的温度尽快恢复正常。同时,建立完善的设备运行状态监测系统,对制冷、加热、风机等关键部件的运行参数进行实时监测,提前预警可能出现的故障,确保测试过程的顺利进行。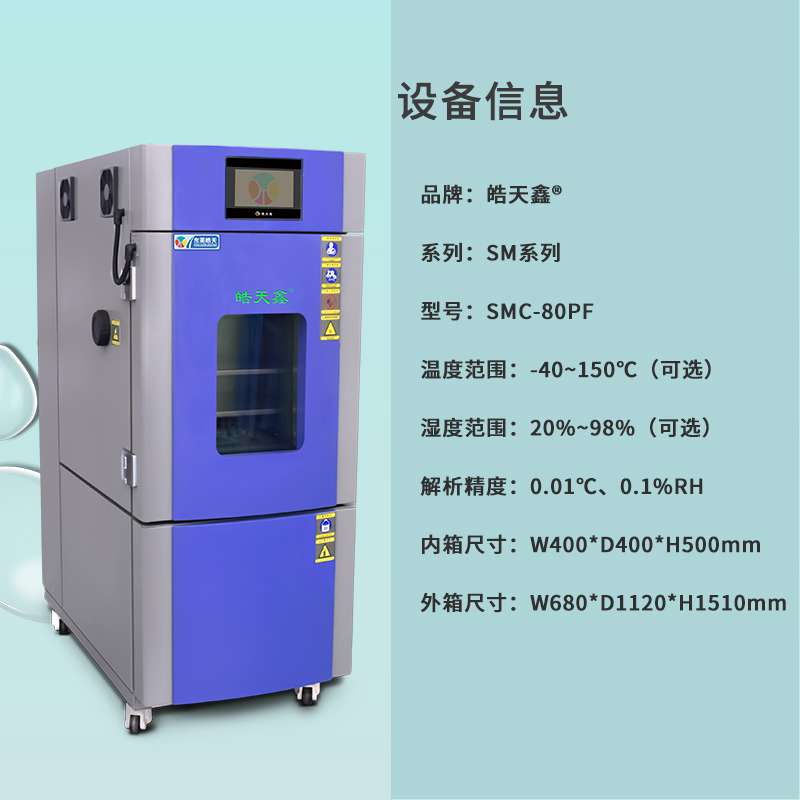
参与评论
登录后参与评论