高温试验在众多领域,如材料科学、电子工业、航空航天等,具有至关重要的作用。它用于评估材料、产品或设备在高温环境下的性能、可靠性和稳定性。而高温试验的原理是实现这一目的的基础,升温速度变化作为试验过程中的关键因素,对高温测试标准有着显著的影响。深入理解这些内容,对于准确执行高温测试、确保试验结果的有效性和可比性具有重要意义。
在高温试验中,热传导是热量传递的一种重要方式。当样品置于高温环境中时,热量通过样品内部的原子或分子相互碰撞和振动进行传递。对于固体材料,热传导系数决定了热量在材料内部传播的速度和效率。不同材料的热传导系数差异较大,例如金属材料通常具有较高的热传导系数,能够较快地将热量均匀分布在整个样品中;而隔热材料的热传导系数较低,热量传递相对缓慢。在高温试验中,热传导过程会影响样品内部的温度分布,进而影响其性能表现。例如,在对电子元器件进行高温试验时,热传导可能导致元器件内部不同部位的温度不均匀,从而影响其电气性能和可靠性。
热辐射是高温试验中另一种重要的传热方式。所有物体都会以电磁波的形式向外发射辐射能,其强度与物体的温度和表面特性有关。在高温环境下,样品会吸收来自周围环境的辐射能,并同时向外界发射自身的辐射能。当吸收的辐射能大于发射的辐射能时,样品温度升高;反之,温度降低。热辐射在高温试验中的特点是无需介质传递热量,可以在真空中进行。例如,在航空航天领域,卫星等设备在太空中会受到太阳辐射等高温环境的影响,此时热辐射是主要的传热方式。在高温试验中,通过控制辐射源的强度和波长等参数,可以模拟不同的高温辐射环境,以测试产品在这种环境下的耐受能力。
对流换热在高温试验中也起着一定的作用,尤其是当试验环境中存在气体或液体介质时。对流换热是指流体与固体表面之间由于温度差异而引起的热量传递过程。根据流体的流动状态,可分为自然对流和强制对流。自然对流是由于流体内部温度不均匀而引起的密度差异,导致流体产生自然流动,从而实现热量传递。强制对流则是通过外部动力(如风机、泵等)使流体以一定的速度流过固体表面,增强热量传递效果。在高温试验箱中,通常会通过循环风机等设备实现空气的强制对流,以保证箱内温度的均匀性。例如,在对大型机械设备进行高温试验时,对流换热可以帮助将热量快速传递到设备的各个部位,使其整体达到设定的高温条件。
相变过程
升温速度的变化会显著影响材料的相变过程。不同的材料在加热过程中会经历不同的相变,如固态到液态的熔化相变、固态到气态的升华相变以及不同晶体结构之间的转变等。当升温速度较快时,材料可能没有足够的时间进行均匀的热量传递和内部结构调整,导致相变温度发生偏移。例如,某些金属材料在快速升温过程中,其熔化温度可能会比在缓慢升温时略高,而且相变过程可能会变得不那么明显,甚至出现过热现象,影响材料的组织结构和性能。
热膨胀系数
材料在高温下会发生热膨胀,其热膨胀系数是衡量材料尺寸随温度变化程度的重要参数。升温速度的不同会导致材料热膨胀过程的差异。快速升温时,材料内部的原子或分子可能来不及均匀地调整位置,从而产生不均匀的热应力。这种热应力可能会导致材料出现裂纹、变形等问题,尤其对于一些热膨胀系数较大且结构复杂的材料更为明显。例如,陶瓷材料在高温试验中,如果升温速度过快,可能由于热应力过大而发生破裂,影响其性能测试结果。
化学反应速率
在高温环境下,材料可能会发生各种化学反应,如氧化、分解等。升温速度的变化会影响化学反应的速率和进程。一般来说,升温速度越快,化学反应的速率也会相应增加。这可能导致材料在高温下的氧化速度加快,从而影响其表面质量和性能。例如,金属材料在高温试验中,快速升温可能会使表面氧化层迅速增厚,改变材料的电学、光学等性能。同时,对于一些需要进行特定化学反应的材料测试,升温速度的变化可能会使反应产物的组成和结构发生改变,影响对材料性能的评估。
传感器响应
高温试验中通常会使用各种传感器来监测温度、压力、湿度等参数。升温速度的变化会影响传感器的响应时间和准确性。快速升温可能使传感器来不及快速准确地感知温度变化,导致测量数据出现偏差。例如,某些温度传感器在快速升温过程中,可能会由于自身的热惯性而不能及时反映样品的实际温度,从而影响对试验温度的控制和监测。此外,升温速度过快还可能对传感器的长期稳定性产生影响,缩短其使用寿命。
加热元件寿命
高温试验设备中的加热元件是实现升温的关键部件。升温速度的变化会对加热元件的寿命产生影响。快速升温会使加热元件在短时间内承受较大的热负荷,导致其温度升高过快。这可能会加速加热元件的老化和损坏,例如加热丝的熔断、加热板的变形等。同时,频繁的快速升温操作也会增加加热元件的热疲劳风险,降低其可靠性和使用寿命。因此,在设计和使用高温试验设备时,需要考虑升温速度对加热元件寿命的影响,合理选择加热元件的材质和规格,并采取适当的保护措施。
控制系统稳定性
升温速度的变化对高温试验设备的控制系统稳定性也提出了挑战。控制系统需要根据设定的升温曲线精确地控制加热功率和温度变化。当升温速度过快或不均匀时,控制系统可能难以及时调整加热参数,导致温度失控。例如,在采用 PID 控制算法的高温试验设备中,如果升温速度超出了控制系统的调节能力范围,可能会使系统出现超调或振荡现象,影响试验的顺利进行和温度控制精度。因此,为了保证控制系统的稳定性和可靠性,需要在设计控制系统时充分考虑升温速度的变化因素,优化控制算法和参数设置。
数据重复性
升温速度的变化会影响高温试验结果的重复性。如果在不同次试验中采用不同的升温速度,可能会导致样品的性能表现出现差异,从而使试验数据的重复性降低。这对于需要进行对比分析和可靠性评估的试验来说是非常不利的。例如,在对某种材料的高温力学性能进行测试时,若一次试验采用快速升温,另一次采用缓慢升温,可能得到不同的强度和韧性数据,使得无法准确判断材料的真实性能和变化规律。因此,为了保证试验结果的可靠性和可重复性,需要在高温测试标准中明确规定合适的升温速度范围,并在试验过程中严格控制升温速度。
误差传播
升温速度的变化还可能导致误差在试验过程中传播和放大。由于升温速度会影响材料的物理化学性质和设备的性能,从而可能引发一系列连锁反应,导致其他测量参数的误差增加。例如,升温速度过快引起的温度不均匀可能会影响样品的尺寸测量精度(由于热膨胀不均匀),进而影响到根据尺寸计算得到的其他性能参数的准确性。这种误差传播可能会使试验结果偏离真实值,影响对产品或材料性能的正确评估。因此,在进行高温试验时,需要充分认识到升温速度变化可能带来的误差传播风险,并采取相应的措施进行控制和修正。
高温测试标准通常对试验箱内或样品表面的温度均匀性有明确规定。升温速度的变化会直接影响温度均匀性。当升温速度较快时,由于热量传递的不均匀性,可能会导致试验箱内不同位置或样品不同部位之间的温度差异增大。为了保证在整个高温试验过程中满足温度均匀性要求,测试标准需要根据不同的升温速度范围制定相应的温度均匀性指标和测试方法。例如,在某些标准中,规定了在特定升温速度下,试验箱内任意两点之间的温度差值不得超过一定限度(如 ±2℃)。同时,还可能要求在试验过程中定期对温度均匀性进行监测和记录,以确保试验结果的有效性。
高温测试标准中还规定了温度偏差的允许范围,即实际测量温度与设定温度之间的允许差值。升温速度的变化会对温度偏差产生影响。快速升温可能导致温度控制系统难以精确跟踪设定温度,从而使实际温度偏离设定值较大。因此,在考虑升温速度因素的情况下,测试标准需要对不同升温速度下的温度偏差允许范围进行合理调整。一般来说,随着升温速度的增加,温度偏差允许范围可能会适当放宽,但必须在保证试验结果可靠性的前提下进行。例如,对于一些对温度精度要求较高的试验,在缓慢升温时,温度偏差允许范围可能为 ±1℃;而在快速升温时,可放宽至 ±3℃。同时,测试标准还可能要求对温度偏差进行实时监测和修正,以确保试验在规定的温度条件下进行。
升温速度的变化会影响高温试验的总时间。较快的升温速度可以缩短达到设定温度所需的时间,但可能会对样品和设备产生不利影响,如前面所述的相变、热应力等问题。因此,高温测试标准需要在综合考虑试验目的、样品特性和设备性能的基础上,合理规定试验时间与升温速度之间的关系。对于一些需要充分观察样品在高温下长期性能变化的试验,可能会要求采用相对较慢的升温速度,并规定较长的试验时间;而对于一些快速筛选或初步评估的试验,可以适当采用较快的升温速度,但需要确保在较短的试验时间内能够获取有代表性的试验结果。例如,在对某种新材料的高温稳定性进行测试时,标准可能规定先以较慢的升温速度(如 1℃/min)将温度升至设定值,然后保持一定时间(如 10 小时)进行观察和测试,以评估其长期稳定性。而在对产品的快速质量检测试验中,可以采用较快的升温速度(如 5℃/min),但试验时间相应缩短,以提高检测效率。
高温试验原理是基于热传导、热辐射和对流换热等方式使样品处于高温环境,以评估其在高温下的性能。升温速度变化作为高温试验中的重要因素,对材料的物理化学性质、设备的性能适应性以及试验结果的可靠性都有着显著的影响。这种影响体现在相变过程、热膨胀系数、化学反应速率、传感器响应、加热元件寿命、控制系统稳定性、数据重复性和误差传播等多个方面。进而,升温速度变化对高温测试标准中的温度均匀性要求、温度偏差允许范围和试验时间规定等方面产生了具体的影响。在制定和执行高温测试标准时,必须充分考虑升温速度变化这一因素,通过合理规定升温速度范围、优化试验设备和控制方法、加强对试验过程的监测和调整等措施,确保高温试验能够科学、准确地进行,为材料研发、产品质量控制和工程应用提供可靠的依据和支持。同时,随着科学技术的不断发展和对高温试验要求的不断提高,还需要进一步深入研究升温速度变化与其他因素之间的相互关系,不断完善高温测试标准,以适应不同领域和应用场景的需求。
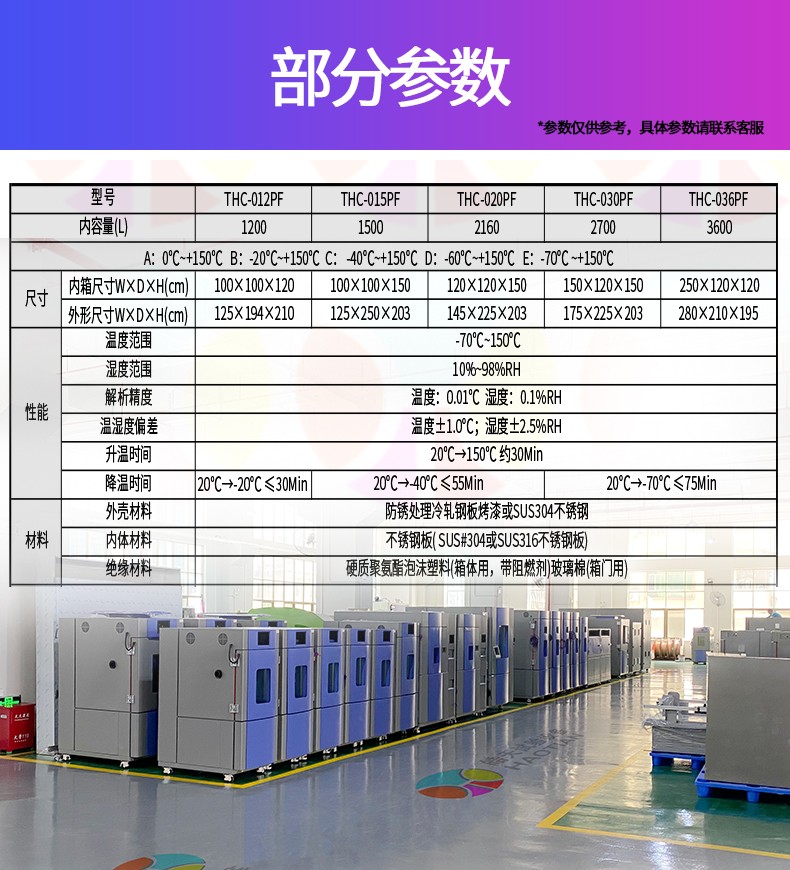
参与评论
登录后参与评论